Over my 27-year career in the e-waste recycling industry, I’ve witnessed many evolutions in processes and technology that have shaped our approach to recycling today. 27 years ago, e-waste recycling was in its infancy. When the WEEE Directive first came into place in 2003, we saw a shift in how businesses and consumers managed their waste. Collection schemes were implemented and targets were set. This was a massive step in the right direction. However, as of today, the US is yet to implement federal programs for e-waste recycling. About half of US states do have recycling programs in place, but without state mandates, we are still seeing low recycling rates across the board.
There have also been developments in technology to find more metals in shredded e-waste streams, ways to find and grade plastics, and recently processes to safely shred li-ion batteries found in very small devices. Additionally, with the growth in companies performing ITAD services, we found a new way to give second life to old electronics. However, beyond this, there have been very few major technological advances.
Until now. I’ve been with for several months now and as we will be starting to build our US operation very soon, I’m genuinely excited by the potential of emerging technologies that are breaking new ground in critical mineral production and e-waste processing.
Below, I share key insights into the current landscape of our industry and the changes I believe are key as we enter a new era of critical metal recovery and e-waste recycling.
The harmful impacts of current solutions
As the focus on global carbon reduction increases, it's no longer sensible to rely on existing solutions known to be extremely carbon-intensive to manage recycling of the circuit boards from e-waste—environmental damage and geopolitical uncertainties are real concerns that can’t be ignored any longer.
Ethically, there is still murkiness in where this waste is actually going and how its dealt with after it leaves our shores. We are making great progress in North America with over 800 R2 certified facilities setting the standard for responsible recycling. However, a significant portion is still shipped to areas of the world unequipped with the proper infrastructure and processes to handle it, causing damage to communities and local environments.
Currently, the only process to recycle circuit boards is to use high-heat methods which are contributing significantly to ecological damage. According to the Department of Energy Advanced Research and Projects Agency-Energy, smelting uses about 4% of the world’s energy and produces about 7% of global greenhouse gas emissions each year, not including the emissions associated with further manufacturing or that of transport necessary to ship waste.
Why Onshore Technology is Crucial
Offshore export of waste is not only costly from an environmental and logistical perspective but exposes us to other significant risks— one being critical metal shortages. When outdated tech leaves our shores, we’re losing the valuable minerals within —and for the world’s biggest technology makers, this risk can directly impact their supply chains. These companies depend on a stable flow of materials, such as copper, to power growing technological advances as well as meet ambitious net-zero targets.
As national critical mineral security concerns grow and natural reserves dwindle, solutions that recover critical metals close to the source make more sense than ever. Demand for green, traceable metals will continue to skyrocket as governments push for renewable technologies like EVs and solar power to reduce carbon emissions.
Reclaiming and reusing these critical metals locally is not just smart; it’s essential. Without the right infrastructure and continuous innovation to reduce reliance on overseas capabilities and carbon-intensive processes, our supply chains remain vulnerable to disruption and more importantly, our planet remains vulnerable to the impacts of increasing carbon emissions. The path forward is crystal clear – we need more sustainable onshore innovations.
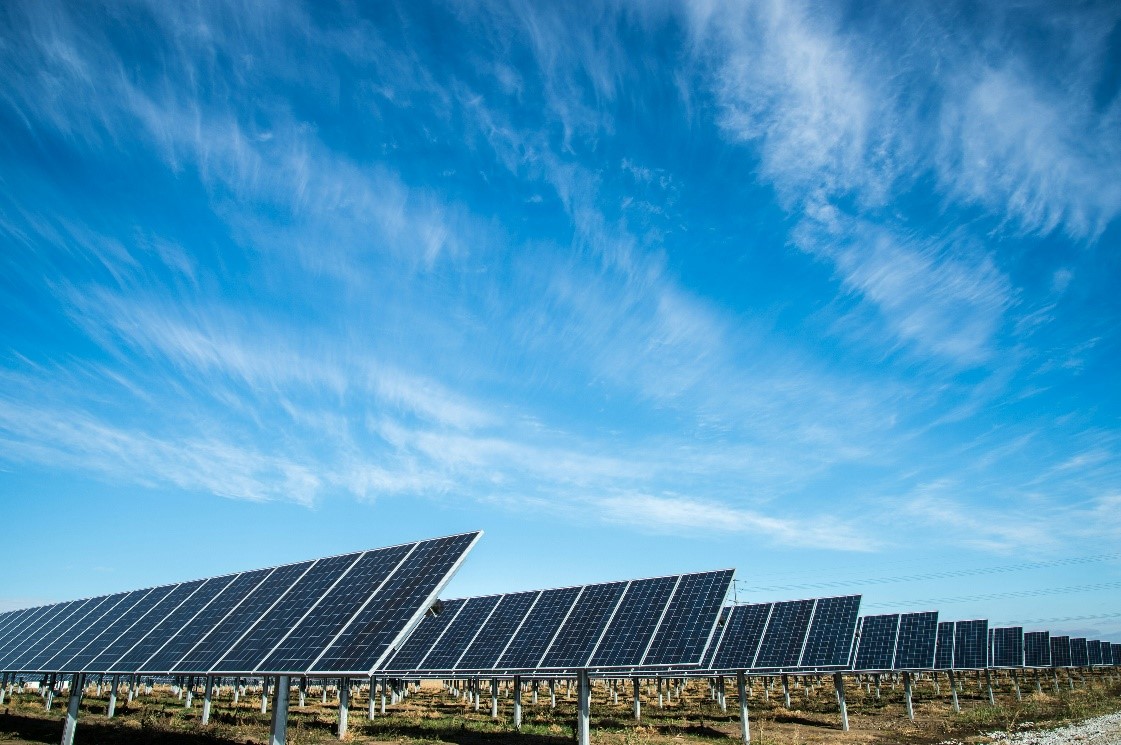
‘Bolt on’ Innovation: The Key to Future-Proofing
Innovating doesn’t mean we need to flip the entire industry on its head. What we need is to strengthen how the industry operates with ‘bolt on’ solutions that can be integrated into the existing supply chain.
Companies like Mint that can offer these flexible, scalable solutions will lead the way. What’s unique about its biotechnology is that its localized and currently produces copper sheets and gold in its low-carbon city-scale facility in Sydney, Australia, removing the need to ship offshore for further refinement. This is key as while many OEMs have take-back programs to recycle old electronics, there remains a broken loop in the chain where materials are still sent offshore for final processing. The ability for Mint to bolt onto an OEM supply chain means the actual metals within these devices are recovered and can be returned directly to the manufacturer. The process involves precise sampling to measure feedstock quality, optimizing returns which are helping to accelerate and achieve true circularity.
Fit-for-purpose solutions like this are what we need – ones that cater to all the players in the industry, from the smaller scale recyclers to the nation's largest technology manufacturers to support them in achieving both economic and environmental goals.
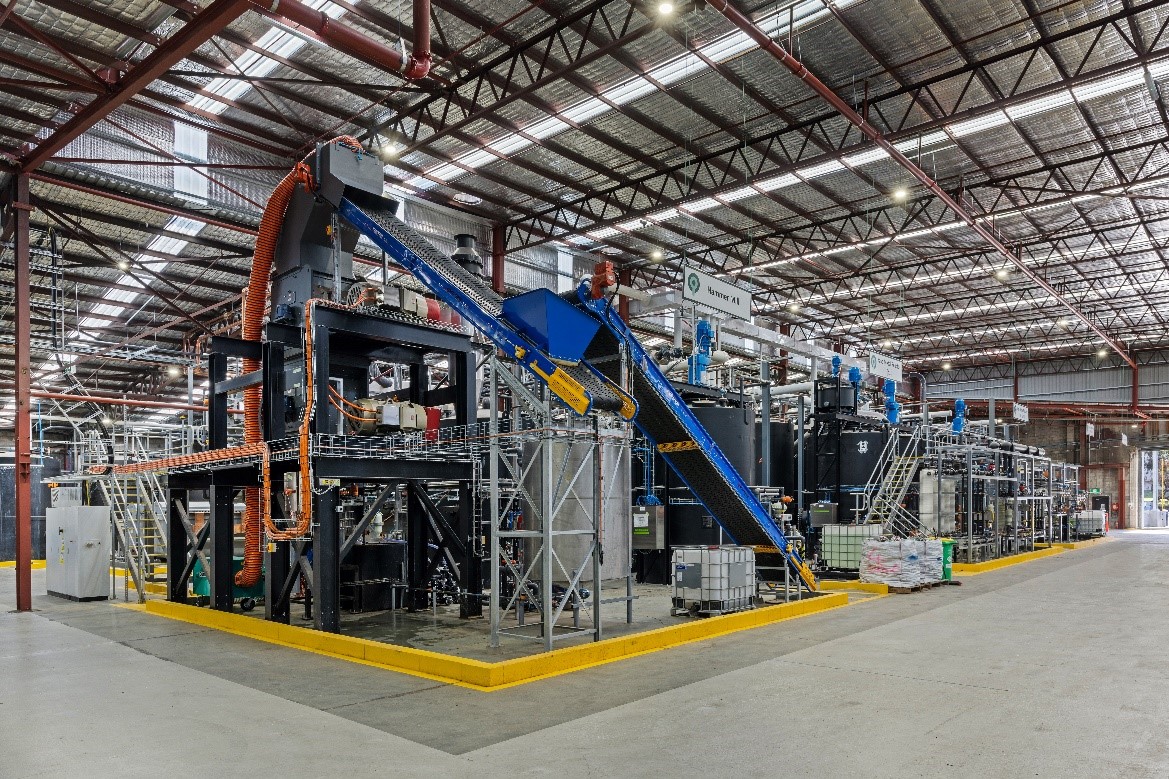
A Cleaner Future Built on Collaboration
We’re facing unprecedented resource challenges, and the need for change reaches far beyond just the e-waste recycling and critical minerals sector. Tech giants have a unique opportunity—and responsibility—to lead the charge by embracing innovation. This isn’t merely about boosting reputation; it’s about safeguarding essential resources, maintaining regulatory compliance, and taking meaningful steps toward a sustainable future.
For this shift to truly make an impact, it must also resonate with the public. While awareness of e-waste challenges is growing, varied policies across U.S. states highlight the need for consistent, collective action. Through collaboration, purposeful innovation, and cohesive policies, we can build a system that efficiently manages e-waste, protects our environment, and keeps critical metals onshore where they’re needed most.
To learn more about strategic partnership opportunities with Mint Innovation, contact hello@mint.bio.